Hydrodynamically and mechanically assisted wet spinning of elastomeric polyurethane filaments
Keywords:
Wet spinning, Polyurethane, Elastomeric, Hydrodynamical stress, FilamentsAbstract
Elastomeric fibers have gained huge interest from material scientists and engineers due to their many potential applications in textiles, composites, smart materials etc. Among the many polymers used in preparation of elastomeric fibers and filaments, polyurethane remains as a very popular choice because of its versatility as a polymer and relative ease of tuning the material properties according to the requirement. Elastomeric polyurethane fibers can be spun using wet, dry and melt spinning processes. However spinning of polyurethane filaments requires fairly expensive, sophisticated equipments that usually have minimum processing capacity in the scale of kilograms. These difficulties have posed problems in carrying out polyurethane fiber related work in typical research labs.In this paper we report a simple method to spin elastomeric polyurethane and polyurethane composite filaments using wet spinning method. The process starts by preparation of polyurethane in solvent or dissolving polyurethane in solvent media. Then the solvent is extruded to a rotating water bath using a hypodermic needle where simultaneous coagulation and drawing occurs. Drawing is induced by hybrid hydrodynamic shear stress and rotation induced tension of the winder. Drawing ratio of the spun fibers was primarily changed by varying the rpm of the winding roller and the rotating water bath. Draw ratios in the range of 2 – 5 could be conveniently achieved by changing the rpm from 5 to 20.
To explain the formation of spun filaments, analytical model and relevant physical parameters are employed that encompasses combined hydrodynamic phenomena of polymer drawing and mechanical drawing. Morphology and the cross section of the spun filaments were evaluated by using Scanning Electron Microscopy (SEM) and filament evenness was assessed using optical microscopy. Surface morphology of the yarns was irregular with number of voids formed due to the rapid diffusion of polymer solvent to coagulating media. At higher draw ratios, periodical variations of the filament cross section occur due to instability of spun polymer. Mechanical properties of spun fibers were evaluated using tensile testing instrument and Dynamic Mechanical Analysis (DMA). Effect of drawing on molecular structure was probed by using both Differential Scanning Calorimeter (DSC) and Fourier Transform Infrared Spectrophotometer. Especially, increase of polymer crystallinity due to drawing could be confirmed by shifting of Tg to higher temperature from -14.36 °C in undrawn polymer to -6.30 °C in drawn filament. It was concluded that the processing feature enables a flexible and facile spinning method to prepare elastomeric polyurethane filaments and can expand the potential applications through research due to ease of producing spun fibers in small quantities.
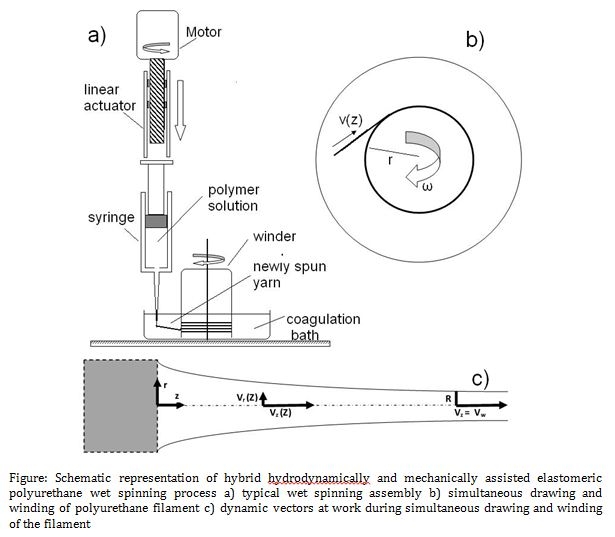
Published
2012-11-27
Issue
Section
Polymer synthesis, characterization and analysis